Новые перспективы для бизнеса в деревообработке
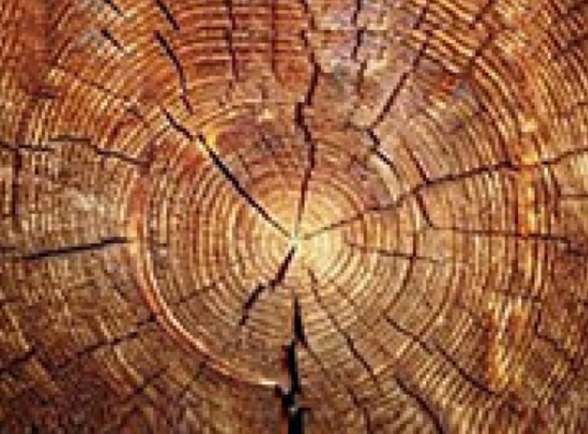
Лесопромышленный и деревообрабатывающий бизнес является одним из наиболее прибыльных: как в части оборачиваемости вложенных средств, так и в части роста прибыльности при укрупнении производства.
Лесоматериалы являются возобновляемым сырьём, спрос на изделия из древесины неуклонно растёт, и рынок постоянно увеличивается, да и лесных ресурсов в России вроде бы хватает…
Предвидя Ваши возражения, уважаемые господа предприниматели, соглашаюсь с ними:
- да, не возобновляем мы лес уже 25 лет, а добраться до качественного «кругляка» не можем, — нет дорог; возить же из-за границы дорого — цены растут не по дням, а по часам;
- да, войти в уже сложившийся лесопромышленный рынок очень трудно: нужны большие административные и финансовые возможности;
- да, потребности этого самого рынка неуклонно растут, но и конкуренция очень жёсткая.
И всё же есть открытые двери и гигантская свободная ниша в лесоторговле и деревообработке.
Первыми вошли в неё фины, а за ними немцы, голландцы, французы, раскрутив производство термомодифицированной древесины (ТМД). Сущность технологии состоит в удалении терморазложением некоторых влаголюбивых химических веществ из древесины, в результате чего можно получить гидрофобную древесину с новыми цветовыми свойствами. Появились крупнейшие фирмы с гигантскими оборотами такие, как Platho (Голландия), Mohlbeck (Австрия), Finnforest и Stora Enso Timber (Финляндия), Thermoholz ( Германия). Ёмкость только российского рынка оценивается специалистами в 100-125 тыс. кубометров в год.
Проявились и недостатки ТМД: цветовая гамма быстро выцветает при солнечном освещении, для получения высококачественной продукции нужны и исходные породы высокого качества (бук, ясень, дуб, тропическая древесина), производство энергозатратно, а отсюда и цены получились немалые. Да и разлагать уже имеющиеся в древесине природные химические компоненты, чтобы обеспечить гидрофобность, надо ли? Ведь плотность и прочность при этом падает, огне-и биостойкость остаются прежними: то есть и горит ТМД так же, как исходная древесина, и гниёт и плесневеет.
Тогда-то и снял Евросоюз запрет на осуществление химической модификации древесины и вплотную приступил к её исследованию и производству. Пока объявлено только о производстве химически модифицированной древесины (ХМД) «Accoya» в Голландии путём ацетилирования и «Kebony» в Норвегии путём фурфулирования исходной древесины. Там уже построены и уникальные мосты, и многоэтажные дома, поскольку по удельной прочности древесина превышает многие марки сталей.
Европейцы, американцы и японцы поняли, что устранить недостатки, а также придать новые полезные свойства такому старому и всем вроде бы всем знакомому материалу, как древесина, можно, просто вводя в массив древесины определённые вещества-модификаторы, которые, реагируя при благоприятных условиях с природными компонентами древесины, позволяют получать новый биокомпозит с заранее задаваемыми эксплуатационными свойствами. Японцы даже собираются использовать модифицированную древесину в космосе…
Кстати интересно: сами поняли или у нас подсмотрели? Ведь модификация древесины активно разрабатывалась, «ГОСТировалась» и применялась в Советском Союзе: «Дестам» для производства подшипников, «Лигнамон» для паркета и мебели (до сих пор производит Словакия).
Ну да, как говорится: «новое — это старое, только всеми забытое». Ведь было же на просторах Союза производство своей ТМД (Минск), ацетилированной модифицированной древесины (Пермь), фурфулированной (Барнаул), а главное, все эти разработки привели к созданию новой технологии, которая, вобрав в себя весь опыт, наконец-то может действительно создавать из любой исходной древесины новую модифицированную древесину, свойства которой задаются при её производстве согласно требованиям заказчика. Это механохимическое модифицирование древесины, при котором недорогой основной модификатор-синергист, вводимый на межклеточный уровень древесного вещества, несёт в себе, при этом многократно усиливая их свойства, незначительное количество специфических функциональных добавок, которые и придают новому материалу нужные свойства. Химическая реакция между модификатором и природными древесными компонентами происходит в массиве древесины под действием давления, температуры и механических усилий. Предварительное название нового биокомпозита — механохимически модифицированная древесина (МХМД).
Именно МХМД является той самой дверцей, которая позволяет найти не занятое пока пространство рынка изделий деревообработки. Объясню,каким образом.
Первое — это сырьё.
При производстве МХМД может использоваться любое древесное сырьё: массив древесины любой породы, горелый лес, топляк, тонкомер, отходы деревообработки, даже солому. При использовании массива (бревно, брус, доска) в качестве исходной древесины экономически более выгодно использовать быстрорастущие «неделовые» породы древесины: осину, тополь, иву, ольху, осокорь, берёзу и т.д. То есть всё то, что пока современным лесозаготовителям в Вашей местности не нужно, потому что не востребовано, и они задёшево отдадут это добро Вам. Если поверить специалистам, то такого добра только в европейской части России более 16 миллионов кубометров! Запасы топляковой древесины в той же европейской части России (по данным ЦНИИ лесосплава) только на действующих лесосплавных реках превышает 9,0 млн. кубометров! Стоимость одного поднятого куба топляка от 500 рублей. Вот это ресурсы! Нужно ещё учесть, что очистка рек — дело архинужное для России. Здесь и родная администрация может профинансировать, а народ спасибо скажет. А предприниматель имеет не просто первосортный лесной сортамент, но ещё и проморёный, который с помощью технологии МХМД можно в чистое золото превратить за рубежом, где он особенно востребован.
Конечно, специалист в вопросах топляковой древесины возразит мне, что отличного сортамента из всего поднятого топляка будет процентов 50%, а остальное — подпорченная и гнилая древесина, корни, коряги… Для технологии МХМД и это – сырьё. Нужно переработать его в опилки и сделать ДСП опять же по технологии МХМД, без применения дорогостоящих смол. По моим подсчётам себестоимость квадратного метра такого ДСП на деревообрабатывающем производстве перерабатывающем всего 160 тонн своих отходов – около 100 рублей.
Вспомогательное сырьё — водный раствор модификатора. Текущий расход воды на техпроцесс незначителен для малого производителя (200-300 кубов МХМД в месяц) и его можно не учитывать при расчёте себестоимости. Более важно, по какой цене приобретать основной модификатор. В моём случае — это карбамид (лучше марки А, он же пищевой), и цены на него колеблются от 11 тысяч рублей за тонну в ООО «Салаватнефтеоргсинтез» и до 38 рублей за килограмм в соседнем магазине. Так что, сколько он Вам встанет в себестоимости МХМД (а нужно иногда до 200 кг на куб), — работа Вашего снабженца. Доля функциональных добавок к основному модификатору незначительна. Они хотя и дороги, но на тонну раствора нужно несколько килограмм.
Второе — это оборудование.
Сразу оговорюсь: оборудование по технологии ТМД использовать можно только для сушки и термообработки МХМД, пропитку же придётся делать диффузионно в ваннах или приобретать для неё специальный автоклав.
Сам техпроцесс механохимического модифицирования древесины заключается в пропитке исходной древесины (поэтому лучше применять сырую свежесрубленную) водным раствором модификатора, сушке пропитанной древесины, её термообработке и уплотнении (если заказчик потребует МХМД малой плотности — вопрос тоже решаем). Все эти процессы можно совместить в одном автоклаве типа АВТРМ (такие раньше на заводах силикатного кирпича употреблялись) или специально заказанном (тогда уж лучше «Scholz» Германия).
Специально оборудование пока никто ещё не выпускает, взялась за проектирование и последующее производство одна нижегородская фирма! Поэтому цену на оборудование МХМД назвать пока затруднительно. Для примера: специально заказанный для выпуска МХМД на российском предприятии автоклав АВТЗМ 2800-10000-12,5 (диаметр — 2,8 м, длина — 10 м), позволяющий выпускать до 450 кубов в месяц, стоил 8,5 млн. рублей.
В качестве примера привожу перечень оборудования для фирмы Х, выпускающей в месяц 250 м3 непрессованного погонажа и 100 м3 прессованных изделий (паркетная доска с плотностью 1100 кг/м3 ):
Третье – затраты на производство изделий из МХМД.
Легко говорить по этому поводу, если речь идёт о раскрученном массовом производстве какой-то давно выпускаемой продукции. Есть статистика и много экономических расчётов. Наш разговор касается нового перспективного производства, «зелёные ростки которого впервые улыбнулись солнцу».
Поэтому опять сошлюсь на расчёты перспективного предприятия Х, выпускающего массивную паркетную доску и облицовочные плиты из отходов собственного производства. Затраты электроэнергии на модификацию одного куба МХМД составляют 200-220 кВт, на мехобработку — традиционно для обработки твёрдых пород древесины. Предполагается ежемесячная поставка обрезной доски в количестве 450м3 по цене 5 000.руб. за куб и карбамида по цене 11 тыс.руб. за тонну.
Предприятие работает круглые сутки, средняя численность работающих — 35 человек.
Расчётная себестоимость кубического метра непрессованной доски МХМД для предприятия Х составляет 11,25 тыс.руб. , а прессованной — 22,5 тыс.руб.. Расчёт произведён из условия, что предприятие имеет один автоклав АВТЗМ 2800-10000 —12,5, специально переоборудованный под техпроцесс МХМД.
Четвёртое — свойства выпускаемой продукции.
Если я Вас ещё не утомил, то давайте вспомним, что основное преимущество МХМД заключено в том, что свойства продукции задаются в процессе производства в соответствии с пожеланиями заказчика или потребителя. Поэтому привожу свойства МХМД осины в сравнении со свойствами исходной древесины деловых пород.
Привожу для примера осину, потому что каждый из нас держал её в руках в виде спичек. Вот только спичка из МХМД осины гореть не будет, потому что этот материал либо быстро затухает сам, если его смогли поджечь, а если нужно — то и не поджигается. И влагу он не очень-то «любит» и жучков и червячков. От традиционных заболеваний древесины (грибки, плесень, гниль) он «привит», а если и были такие в исходной древесине (например синяя гниль), то технология МХМД это излечивает (от синей гнили остаются лишь серо-чёрные штрихи).
Отмечу ещё некоторые индивидуальные свойства МХМД:
- её можно гнуть в самых неожиданных плоскостях;
- получать изображения типа интарсии или голографии, рельефные изображения с прямыми и острыми углами и высотой рельефа 10 мм прессованием;
- изменять произвольно текстуру и цвет исходной древесины;
- увеличивать плотность более 2000 кг/м3 , что влечёт за собой прямопропорциональное увеличение прочности, твёрдости и истираемости;
- производить прессованные срощенные по технологии армирования силовой решёткой щиты теоретически неограниченных размеров, не применяя при этом прессового оборудования.
А сколько свойств этого материала 21 века мы ещё не открыли, сколько технологических возможностей ещё не выявили, сколько новых видов изделий из него ещё будет придумано? Отвечу сразу господам скептикам: да, изделия из МХМД серийно пока не выпускаются (ну разве что корпуса барометров ОАО «Утёс»), но то, что Вы видите на фото, сделано и снято автором статьи, и Вы можете с его согласия всё это потрогать и пощупать.
Пятое — рынок изделий из МХМД.
В общем-то он традиционен:
- стройиндустрия: деревянные элементы помещений, покрытия, перекрытия и сами дома;
- судо-, вагоно- и машиностроение;
- мебельная промышленность;
- ограждения и загоны для с/х животных;
- бытовые изделия: инструменты, кухонные принадлежности, декоративные элементы, ритуальные принадлежности, и прочее;
- тара и упаковка;
- сувенирные изделия и бижутерия;
- спортивные изделия и инвентарь;
- музыкальные инструменты;
- сваи для дамб, шахт и градирен;
- опоры и шпалеры для садов, ландшафтные сооружения;
- строительная опалубка;
- прочие новые изделия.
Выбирайте любой вид изделий, и смело предлагайте тому потребителю, нужды которого Вы уже знаете. Продукция из МХМД создает уникальное предложение на рынке: качество материала на уровне лучших пород твердой древесины при цене ниже, чем пиломатериалы из твердых пород древесины, уже имеющиеся на рынке. Плюс новые эксплутационные свойства и новые технологические возможности.
Экологи и администрация Вами не нахвалятся — продукция и производство экологически чисты, а лесоповал в районе применения такой технологии должен быть девственно чист. Всё, что там было, — потенциальное сырьё для МХМД. А это означает благоприятственное продвижение в рынок.
Производство изделий из МХМД основано на применении экологически чистого сырья и материалов, оно безотходно и может перерабатывать отходы других деревообрабатывающих производств, даже такие, как отходы, возникающие при механической обработке на производстве листов ДСП. Оно легко встраивается в технологический цикл любого деревообрабатывающего предприятия и резко повышает его конкурентноспособность.
Из-за объективных причин «первопроходцам», конечно, придётся позиционировать этот товар на рынке и нести определённые расходы: как по сертификации, так и по рекламе. Но новичкам везет — они впоследствии станут законодателями на этом стремительно расширяющемся рынке.
Подробнее с разработками по МХМД можно ознакомиться в Интернете, набрав в поисковике фразу «механохимически модифицированная древесина».
Задать вопросы автору можно по адресу: vk58@yandex.ru.